Process Mining for Telehealth improvement— a case for Healthcare Operations
Process management in telemedicine continues to present significant challenges. The creation of a "current state" representation of existing processes and the connection between business processes and the organization's enterprise information systems are two significant problems that process mining, a relatively new and cutting-edge technology, can help address.

Telehealth has been embraced by the Danish health system as a way of providing an aging population with better service and quality of life when treating chronic diseases at home. This objective will require a set of additional processes in traditional healthcare logistics, such as the need for delivery of pharmaceuticals, equipment, or physiological tests for specialized analysis to and from the patient's home, all while maintaining and improving service delivery. This will require quick and convenient delivery and other specialized logistic capabilities, such as traceability, cold chains, and a controlled maximum delivery time of samples to testing facilities, for example.
As these increased logistics requirements will require a sharp learning curve, they will need to be based on solid operations and effective process management. Here, process improvement is a crucial activity that involves modifying processes from their present structure to one that is somehow better. However, complex organizations in numerous industries, including healthcare, have identified at least two significant general issues with this activity.
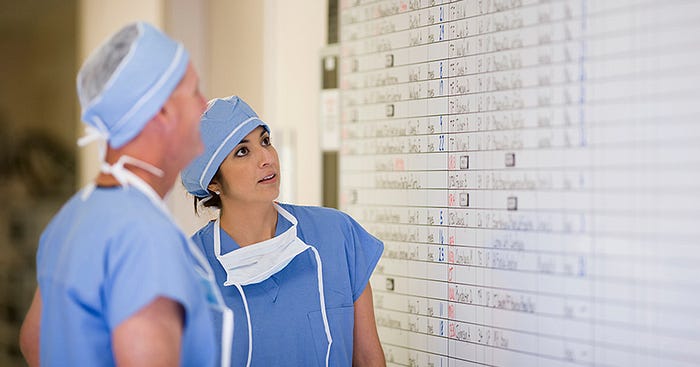
Process management in healthcare presents at least two important challenges, the represention of the current way of performing processes, and a lack of active connection between these processes and the process data in existing information systems.
A first problem: representing current state of activities
A first general problem involves the description of “current state” processes—a representation of how an operational process is being performed today. In process reengineering (a disruptive or radical improvement approach), organizations are primarily interested in an improved “to be” process, so often they have little interest in exploring “as is,” or how the process is currently performed. However, understanding the current process is critical to knowing whether it is worth investing in improvements, where performance problems exist, and how much variation there is in current processes across the organization. As a result, process improvement projects tend to either skip the current “as is” analysis altogether, adopt shortcuts to it, or pay onerous external consultants to analyze these “as is” processes.
On the other hand, organizations that adopt an incremental improvement approach tend to spend too much time analyzing the “as-is,” frequently basing this description on interviews and sticky notes, which executives sometimes regard as overly subjective and treat with justifiable skepticism.
Another problem: conecting processes to their data
The other general problem with process management is the lack of connections between business processes and the data about these processes in the organization’s information systems. Some enterprise systems (SAP, for example) are process-oriented in the sense that they support processes like order-to-cash or procure-to-pay, but there is rarely an easy way to understand how the process is being executed from the information system. Aspects of process design are supported by a variety of technologies, including Microsoft Visio and Aris from Software AG. However, if you need details about how your process is operating on a daily basis, you will typically need to perform a challenging set of manual data collection and analysis steps. Additionally, many process improvement approaches—Lean and Six Sigma, for example—have not emphasized information technologies as enablers of processes or of process management.

Process Mining’s potential in heathcare
Process mining uses information from healthcare transaction systems and provides detailed, data-driven information about how key processes are structured and how they are performing. When a process is digitalized, event logs are continuously created as work is completed. For instance, when an order is received, a product is transported from the supplier, delivered to the healthcare facility, and delivered inside the hospital.
These logs represent how computer-mediated work is really happening, including, among others, who did it, the resources it required, how long it took, and how it departed from the average, for example. Process analytics creates key performance indicators for the process and any of its subparts, which enables healthcare operations to focus, for example, on the improvement of the highest priority process steps first. Additionally, AI algorithms can detect the root causes of variation, and identify patterns of operation that are likely to lead to bigger problems. At the same time, process mining reinforces a commitment to data-driven and AI-assisted decision making in Danish healthcare.
The selection of where to apply process mining is important. Healthcare Systems will get the best value from applying it to processes that have been digitized and are supported by an IT system, yet where there is still some unstructured work (i.e. reviews and approvals) that happens outside of the IT system.
Process mining’s capabilities are therefore extremely useful for anyone whose job it is to oversee, improve, or troubleshoot operational processes. Through process mining, the development of current-state process flows is automatic and no longer labor-intensive. Even if you’re not concerned with process management overall or the state of the broad process in which you work, you can find out what’s happening in your little piece of it and fix any problems by using the available process data.

Process mining may not be for everyone, yet large, complex healthcare organizations with a commitment to quality and an interest in internal benchmarking can best benefit from the transparency it creates. However, if an organization isn’t oriented toward process management, it probably won’t do well with process mining.
Additionally AI algorithms can detect the root causes of variation, and identify patterns of operation that are likely to lead to bigger problems.
Process mining depicts a visually appealing and a data-based view of process performance. This should attract the interest of senior managers in healthcare organizations, who can easily see where problems and opportunities lie, reinforcing a commitment to data-driven and AI-assisted decision making in Danish healthcare.